Data Reconciliation
Understanding Data Reconciliation in Industrial Context
Data reconciliation addresses the inevitable inconsistencies that arise when industrial systems collect, process, and store data from multiple sources. These discrepancies can result from sensor calibration differences, network delays, system downtime, or varying data collection frequencies across different operational systems.
Unlike simple data validation, reconciliation involves intelligent comparison and correction processes that account for expected variations while identifying and resolving significant discrepancies. This process is essential in industrial environments where data from SCADA systems, historians, and MES systems must align to provide accurate operational visibility.
Types of Data Reconciliation
Temporal Reconciliation
Aligns data across different time periods, accounting for clock drift, time zone differences, and varying sampling frequencies between systems.
Cross-system Reconciliation
Compares and aligns data from different industrial systems, such as reconciling production counts from manufacturing execution systems with inventory management systems.
Measurement Reconciliation
Validates and corrects measurement data from multiple sensors or instruments monitoring the same process parameter, accounting for calibration differences and measurement uncertainties.
Material Balance Reconciliation
Ensures conservation laws are maintained across industrial processes, verifying that material inputs, outputs, and accumulation balance according to physical constraints.
Reconciliation Process Architecture
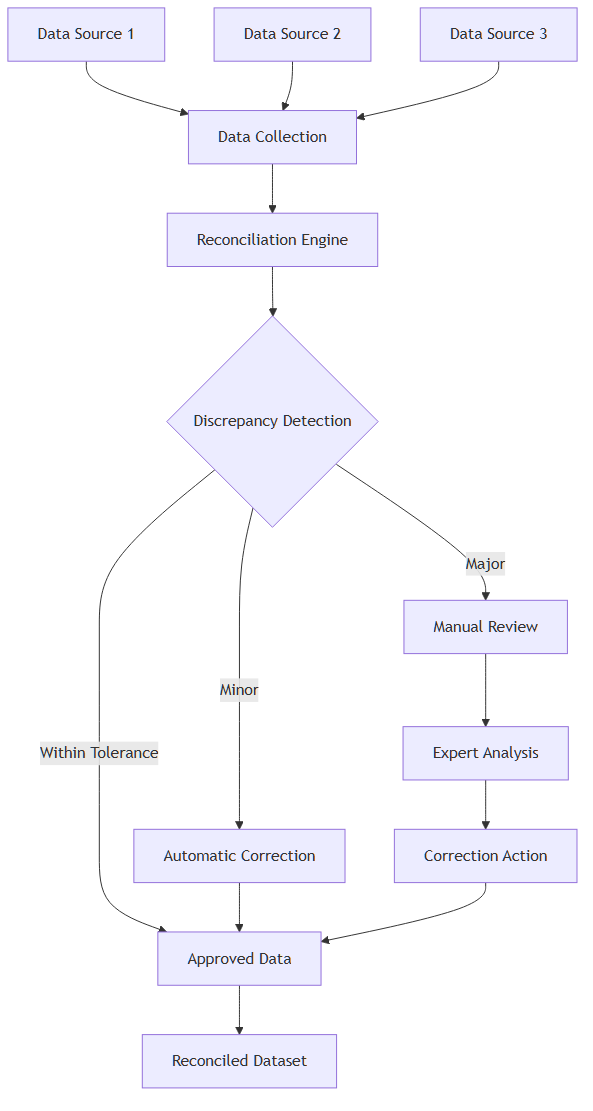
Applications in Industrial Operations
Production Reporting
Manufacturing systems reconcile production data from multiple sources including machine counters, operator reports, and quality control systems to generate accurate production reports and KPIs.
Energy Management
Energy reconciliation compares utility meter readings with sub-meter measurements and calculated energy consumption to identify losses, improve efficiency, and validate billing accuracy.
Financial Reconciliation
Industrial operations reconcile operational data with financial systems to ensure accurate cost accounting, inventory valuation, and performance measurement.
Regulatory Compliance
Process industries reconcile emissions data, waste generation measurements, and safety incident reports across multiple systems to ensure regulatory compliance and accurate reporting.
Implementation Strategies
Rule-based Reconciliation
Implements predefined business rules and tolerance limits to automatically identify and correct common discrepancies:
def reconcile_production_data(line_data, mes_data, threshold=0.05):
"""
Reconcile production counts between line sensors and MES
"""
discrepancy = abs(line_data.count - mes_data.count) / line_data.count
if discrepancy <= threshold:
return create_reconciled_record(line_data, mes_data, 'approved')
elif discrepancy <= 2 * threshold:
# Apply weighted average based on data confidence
reconciled_count = (line_data.count * line_data.confidence +
mes_data.count * mes_data.confidence) / \
(line_data.confidence + mes_data.confidence)
return create_reconciled_record(None, None, 'reconciled', reconciled_count)
else:
return create_reconciled_record(line_data, mes_data, 'review_required')
Statistical Reconciliation
Uses statistical methods to identify outliers and apply correction factors based on historical patterns and measurement uncertainties.
Machine Learning Approaches
Advanced reconciliation systems use machine learning to identify patterns in discrepancies and predict optimal correction strategies based on historical reconciliation outcomes.
Best Practices for Industrial Data Reconciliation
1. Define Clear Reconciliation Policies
- Establish tolerance levels for different data types
- Define escalation procedures for significant discrepancies
- Document reconciliation rules and decision criteria
2. Implement Automated Monitoring
- Monitor reconciliation success rates and patterns
- Alert on recurring discrepancies requiring investigation
- Track reconciliation performance metrics
3. Maintain Audit Trails
- Record all reconciliation actions and decisions
- Maintain version history of reconciled data
- Implement approval workflows for manual corrections
4. Ensure Data Quality at Source
- Implement upstream data validation
- Maintain consistent calibration across measurement systems
- Standardize data collection procedures
Reconciliation in Real-time Systems
Streaming Reconciliation
Modern industrial systems implement real-time reconciliation using stream processing frameworks to detect and correct discrepancies as data flows through the system.
Near Real-time Correction
Systems implement near real-time reconciliation for critical operational parameters while using batch reconciliation for comprehensive historical data validation.
Event-driven Reconciliation
Triggered reconciliation processes respond to specific events such as shift changes, equipment maintenance, or production line configurations.
Integration with Data Governance
Data Quality Framework
Reconciliation integrates with broader data governance frameworks to ensure consistent data quality policies across industrial operations.
Master Data Management
Reconciliation processes leverage master data management systems to ensure consistent reference data across all reconciliation activities.
Data Lineage Tracking
Reconciliation systems maintain detailed data provenance information to track the origin and transformation of reconciled data.
Advanced Reconciliation Techniques
Predictive Reconciliation
Uses historical patterns and machine learning to predict likely discrepancies and proactively adjust reconciliation parameters.
Multi-dimensional Reconciliation
Simultaneously reconciles data across multiple dimensions such as time, location, product type, and measurement type.
Constraint-based Reconciliation
Applies physical and business constraints to guide reconciliation decisions, ensuring results comply with operational and scientific principles.
Performance Considerations
Scalability Requirements
Reconciliation systems must handle increasing data volumes from expanding industrial operations while maintaining acceptable processing times.
Processing Optimization
- Implement parallel processing for independent reconciliation tasks
- Use efficient algorithms for large-scale data comparison
- Optimize database queries for reconciliation operations
Resource Management
- Balance reconciliation frequency with system resources
- Implement priority-based reconciliation for critical data
- Plan for peak processing periods
Challenges and Solutions
Data Volume Scaling
Large industrial operations generate massive data volumes requiring sophisticated reconciliation architectures and efficient processing strategies.
Real-time Requirements
Balancing thoroughness of reconciliation with real-time processing requirements demands careful system design and optimization.
Complex Interdependencies
Industrial data often has complex relationships requiring sophisticated reconciliation logic and domain expertise.
Related Concepts
Data reconciliation works closely with data integrity, data quality management, and data validation processes. It integrates with change data capture systems and supports operational analytics requirements in industrial environments.
Modern reconciliation systems increasingly leverage artificial intelligence and machine learning techniques to improve accuracy and reduce manual intervention requirements.
What’s a Rich Text element?
The rich text element allows you to create and format headings, paragraphs, blockquotes, images, and video all in one place instead of having to add and format them individually. Just double-click and easily create content.
Static and dynamic content editing
A rich text element can be used with static or dynamic content. For static content, just drop it into any page and begin editing. For dynamic content, add a rich text field to any collection and then connect a rich text element to that field in the settings panel. Voila!
How to customize formatting for each rich text
Headings, paragraphs, blockquotes, figures, images, and figure captions can all be styled after a class is added to the rich text element using the "When inside of" nested selector system.