Telemetry Data
Core Characteristics
Telemetry data exhibits several distinctive characteristics that make it particularly valuable for industrial applications:
- Temporal Structure: Data points are timestamped and collected at regular intervals, enabling trend analysis and historical comparisons
- Automated Collection: Systems generate data without human intervention, ensuring continuous monitoring of critical parameters
- High Volume: Industrial systems can generate millions of data points per day from multiple sensors and equipment
- Real-time Transmission: Data is transmitted to central systems for immediate analysis and alerting
Types of Industrial Telemetry Data
Equipment Performance Metrics
These include operational parameters such as motor speeds, temperatures, pressures, and vibration levels from manufacturing equipment, providing insights into equipment health and efficiency.
Environmental Conditions
Temperature, humidity, air quality, and other environmental factors that affect production processes and equipment performance.
Process Parameters
Variables that directly impact product quality, such as flow rates, chemical concentrations, and processing times in manufacturing operations.
System Health Indicators
Status information about control systems, network connectivity, and infrastructure components that support industrial operations.
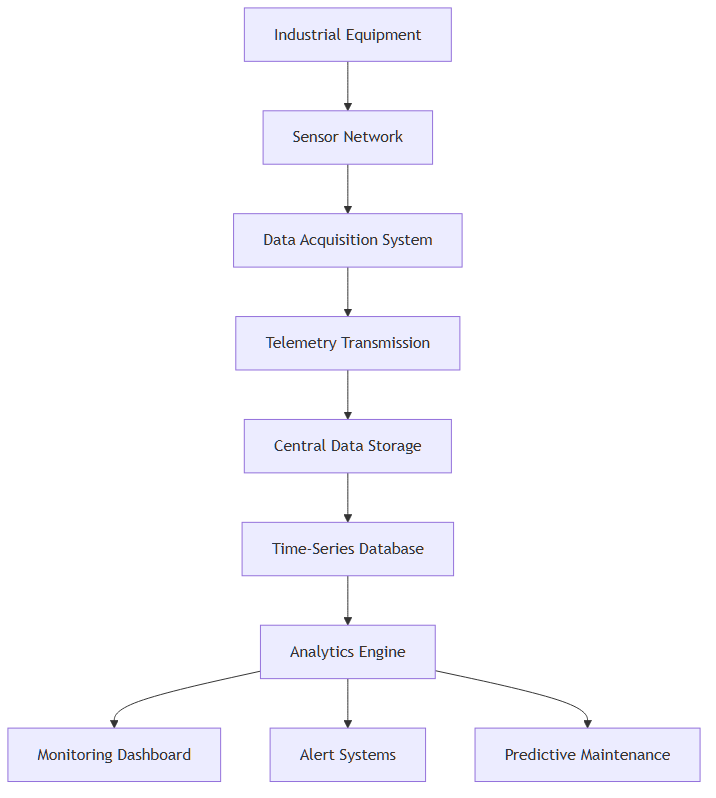
Applications in Industrial R&D
Design Validation
Telemetry data from prototype testing and field trials provides crucial feedback for validating design assumptions and refining simulation models used in product development.
Performance Optimization
By analyzing telemetry data from production systems, engineers can identify bottlenecks, optimize process parameters, and improve overall system efficiency.
Predictive Maintenance
Continuous monitoring of equipment telemetry enables early detection of potential failures, reducing unplanned downtime and maintenance costs.
Quality Control
Real-time telemetry data helps maintain product quality by monitoring critical process parameters and triggering corrective actions when deviations occur.
Data Collection and Transmission
Collection Methods
Industrial telemetry systems typically employ distributed sensor networks connected to programmable logic controllers (PLCs), data acquisition systems, or edge computing devices that aggregate and prepare data for transmission.
Transmission Protocols
Common protocols include MQTT for lightweight messaging, OPC UA for industrial automation, and HTTP/REST for web-based applications. The choice depends on factors such as network reliability, security requirements, and data volume.
Data Formats
Telemetry data is often encoded in compact binary formats or structured formats like JSON to minimize transmission overhead while maintaining readability for analysis tools.
Storage and Management
Time-Series Databases
Industrial telemetry data is typically stored in specialized time-series databases optimized for high-throughput ingestion and time-based queries.
Data Retention Policies
Organizations implement telemetry retention strategies that balance storage costs with regulatory requirements and operational needs.
Data Compression
Advanced compression algorithms reduce storage requirements while maintaining data integrity for historical analysis and compliance reporting.
Best Practices
- Implement proper data governance to ensure data quality and consistency across multiple telemetry sources
- Design for scalability to handle increasing data volumes as industrial systems expand
- Establish security protocols to protect sensitive operational data during transmission and storage
- Plan retention strategies that comply with regulatory requirements while managing storage costs
- Implement data validation to identify and handle sensor malfunctions or transmission errors
- Design efficient querying patterns that take advantage of time-series database capabilities
Performance Considerations
Telemetry data systems must handle high-frequency data ingestion while providing low-latency access for real-time monitoring and alerting. Key performance factors include network bandwidth, storage I/O capacity, and query optimization for time-based analysis patterns common in industrial applications.
Modern industrial telemetry systems often implement edge computing architectures that perform local processing and aggregation, reducing network bandwidth requirements and improving response times for critical control loops.
What’s a Rich Text element?
The rich text element allows you to create and format headings, paragraphs, blockquotes, images, and video all in one place instead of having to add and format them individually. Just double-click and easily create content.
Static and dynamic content editing
A rich text element can be used with static or dynamic content. For static content, just drop it into any page and begin editing. For dynamic content, add a rich text field to any collection and then connect a rich text element to that field in the settings panel. Voila!
How to customize formatting for each rich text
Headings, paragraphs, blockquotes, figures, images, and figure captions can all be styled after a class is added to the rich text element using the "When inside of" nested selector system.