Industrial Process Control Data
Understanding Process Control Data Fundamentals
Industrial process control data emerges from the continuous monitoring and management of complex manufacturing processes where precise control of variables such as temperature, pressure, flow rates, and chemical concentrations directly impacts product quality and operational safety. This data originates from sophisticated control systems including Distributed Control Systems (DCS), Programmable Logic Controllers (PLCs), and SCADA networks that form the backbone of modern industrial automation.
The fundamental purpose of process control data extends beyond simple monitoring to enable closed-loop control systems where real-time measurements automatically adjust process parameters to maintain optimal operating conditions, supporting Model Based Design principles and advanced control strategies.
Core Components and Data Types
Industrial process control data encompasses several critical categories of information:
- Process Variables: Temperature, pressure, flow rates, level measurements, and chemical concentrations
- Control Outputs: Valve positions, motor speeds, heater settings, and actuator commands
- Setpoints and Targets: Desired operating values and control parameters
- Alarm and Event Data: System alerts, operator actions, and state changes
- Quality Measurements: Product specifications, test results, and compliance metrics
- Equipment Status: Operational modes, health indicators, and maintenance requirements
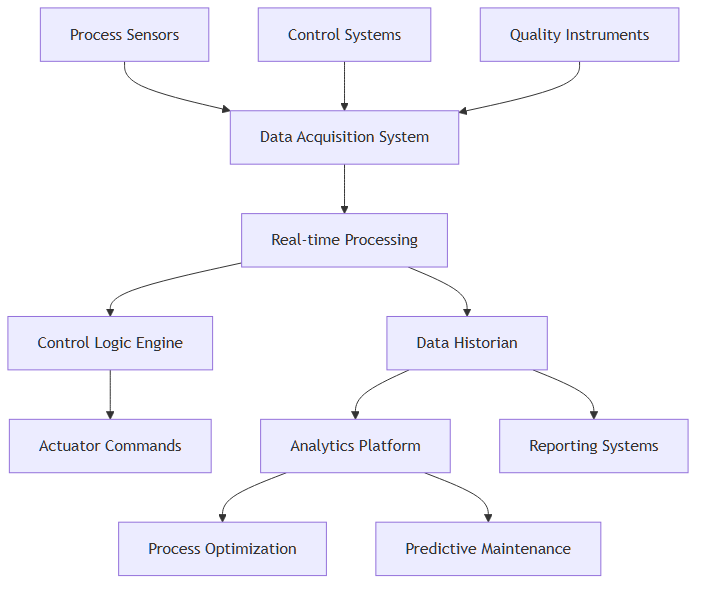
Applications in Industrial Operations
Real-time Process Control
Process control data enables sophisticated control algorithms that automatically adjust operating parameters to maintain optimal conditions. Advanced control strategies such as Model Predictive Control (MPC) utilize historical process data to predict future behavior and optimize control actions.
Quality Management
Manufacturing processes rely on process control data to ensure product quality through Statistical Process Control (SPC) methodologies, real-time quality monitoring, and automated rejection of out-of-specification products.
Equipment Optimization
Process control data supports equipment performance optimization through analysis of operating efficiency, energy consumption patterns, and equipment utilization rates, enabling data-driven decisions for process improvements.
Regulatory Compliance
Industries such as pharmaceuticals, food processing, and chemicals utilize process control data to maintain detailed records required for regulatory compliance, batch genealogy tracking, and audit trail documentation.
Data Management and Storage Architecture
Time-series Optimization: Process control data requires specialized storage systems optimized for time-series patterns, with high-speed ingestion capabilities and efficient compression algorithms designed for industrial data characteristics.
Real-time Processing: Control systems demand sub-second response times, requiring edge computing capabilities and real-time data processing pipelines that can handle high-frequency updates without introducing latency.
Data Integration: Modern process control systems integrate data from multiple sources including legacy DCS systems, modern IoT sensors, and laboratory information management systems (LIMS).
Performance and Scalability Considerations
Data Acquisition Rates: Industrial facilities may generate hundreds of thousands of data points per second, requiring robust ingestion systems capable of handling peak loads without data loss.
Storage Requirements: Long-term data retention for regulatory compliance and historical analysis necessitates efficient storage architectures with automated archival policies.
Query Performance: Real-time dashboards and control applications require sub-second query response times across large historical datasets.
Best Practices for Implementation
- Data Architecture Design: Implement hierarchical data structures that reflect plant organization and process relationships
- Security Framework: Establish robust cybersecurity measures to protect critical process control data from unauthorized access
- Data Quality Management: Implement validation rules and quality checks to ensure data integrity and reliability
- Backup and Recovery: Design comprehensive backup strategies for mission-critical process control data
- Performance Monitoring: Continuously monitor system performance and data quality metrics
- Documentation Standards: Maintain clear documentation of data sources, processing logic, and system configurations
Implementation Example
# Example process control data configuration
process_config:
control_loops:
- name: reactor_temperature
setpoint: 350.0
measurement_tag: TI_001
output_tag: TIC_001_OUT
scan_rate: 100ms
- name: flow_control
setpoint: 1500.0
measurement_tag: FI_002
output_tag: FIC_002_OUT
scan_rate: 250ms
data_retention:
real_time: 7d
historical: 10y
compliance: permanent
Integration with Advanced Technologies
Machine Learning Integration: Process control data feeds machine learning models for predictive maintenance, quality prediction, and process optimization algorithms that continuously improve manufacturing performance.
Digital Twin Applications: Real-time process control data synchronizes digital twin models with actual plant conditions, enabling virtual process optimization and scenario analysis.
Cloud Integration: Hybrid architectures combine on-premises control systems with cloud-based analytics platforms for advanced data processing and enterprise-wide visibility.
Related Concepts
Industrial process control data intersects closely with Industrial Data Historian systems, sensor data processing, and Industrial IoT architectures. Understanding these relationships is essential for designing comprehensive industrial automation systems.
Industrial process control data represents the nervous system of modern manufacturing, providing the real-time visibility and control capabilities necessary for safe, efficient, and profitable industrial operations in increasingly competitive global markets.
What’s a Rich Text element?
The rich text element allows you to create and format headings, paragraphs, blockquotes, images, and video all in one place instead of having to add and format them individually. Just double-click and easily create content.
Static and dynamic content editing
A rich text element can be used with static or dynamic content. For static content, just drop it into any page and begin editing. For dynamic content, add a rich text field to any collection and then connect a rich text element to that field in the settings panel. Voila!
How to customize formatting for each rich text
Headings, paragraphs, blockquotes, figures, images, and figure captions can all be styled after a class is added to the rich text element using the "When inside of" nested selector system.