Industrial Data Collection
Core Fundamentals
Industrial data collection operates as the foundation of modern data-driven manufacturing by systematically capturing information from operational systems, equipment, and processes. The process transforms physical phenomena and system states into digital information that can be stored, analyzed, and acted upon by computer systems and human operators.
The fundamental challenge in industrial data collection lies in handling the diversity of data sources, communication protocols, and data formats present in manufacturing environments. Modern facilities contain equipment from multiple vendors spanning decades of technology evolution, requiring sophisticated integration approaches that can handle legacy systems alongside modern IoT devices.
Effective industrial data collection must balance completeness against efficiency, capturing sufficient information to support analytical requirements while minimizing system impact and communication overhead. This balance requires careful consideration of sampling rates, data prioritization, and storage strategies.
Data Collection Architecture
Industrial data collection systems comprise several interconnected components:
- Data Sources: Equipment, sensors, control systems, and enterprise applications that generate operational data
- Acquisition Layer: Hardware and software interfaces that connect to data sources and extract information
- Communication Infrastructure: Networks and protocols that transport data from sources to collection systems
- Processing Layer: Systems that validate, filter, and transform raw data into usable formats
- Storage Systems: Databases and repositories that provide persistent storage for collected data
- Integration Layer: Interfaces that make collected data available to analytical applications and business systems
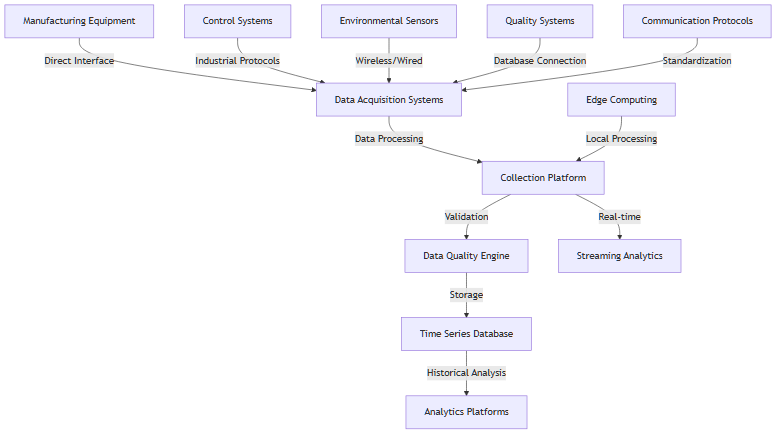
Data Source Types and Characteristics
Equipment and Machine Data
Manufacturing equipment generates diverse data types including operational parameters, performance metrics, alarm conditions, and diagnostic information. This data often requires real-time collection to support immediate decision-making and automated control responses.
Process Variables
Chemical, pharmaceutical, and other process industries require continuous monitoring of process variables including temperature, pressure, flow rates, and chemical composition. These measurements demand high accuracy and precise timing to ensure product quality and safety compliance.
Quality and Inspection Data
Quality control systems generate measurement data from coordinate measuring machines, vision systems, and laboratory instruments. This data requires careful handling to maintain traceability and support statistical process control and continuous improvement initiatives.
Communication Protocols and Standards
Industrial Ethernet: Modern data collection systems leverage industrial Ethernet protocols including EtherNet/IP, PROFINET, and EtherCAT for high-speed, deterministic communication with manufacturing equipment. These protocols provide real-time performance with built-in diagnostic capabilities.
Legacy Protocol Support: Existing equipment often uses legacy protocols including Modbus, DeviceNet, and proprietary communication standards. Data collection systems must provide gateway capabilities that translate between legacy and modern protocols.
Wireless Technologies: Industrial wireless solutions including WirelessHART, ISA100, and private LTE enable data collection from mobile equipment and remote locations. Wireless technologies must address reliability, security, and power management requirements specific to industrial environments.
Real-Time vs. Historical Data Collection
Real-Time Collection: Time-critical applications require immediate data access with minimal latency for control, safety, and optimization purposes. Real-time collection systems prioritize responsiveness and deterministic behavior over comprehensive data capture.
Historical Collection: Analytical applications benefit from comprehensive historical data that provides context for trend analysis, performance optimization, and predictive modeling. Historical collection systems emphasize data completeness, quality, and long-term storage efficiency.
Hybrid Approaches: Modern data collection systems often implement hybrid architectures that provide both real-time access for immediate needs and historical storage for analytical applications. Edge computing and intelligent data routing support these dual requirements.
Data Quality and Validation
Automatic Validation: Industrial data collection systems implement automated validation procedures that identify sensor malfunctions, communication errors, and data quality issues. These procedures include range checking, rate-of-change analysis, and consistency verification across related measurements.
Calibration Management: Systematic calibration procedures ensure measurement accuracy throughout the data collection lifecycle. Automated calibration tracking and drift detection help maintain data quality while supporting regulatory compliance requirements.
Error Handling: Robust error handling procedures address communication failures, sensor malfunctions, and system disruptions while maintaining data collection continuity. Graceful degradation and recovery mechanisms minimize data loss during system issues.
Edge Computing and Local Processing
Edge Data Processing: Modern industrial data collection increasingly leverages edge computing capabilities that process data locally before transmission to central systems. Edge processing reduces bandwidth requirements while enabling immediate local responses to operational conditions.
Data Filtering and Aggregation: Intelligent edge systems filter and aggregate data based on operational relevance and analytical requirements. This processing reduces data volumes while preserving essential information for decision-making purposes.
Local Storage: Edge systems provide local data storage capabilities that ensure data preservation during communication outages and support offline analysis and troubleshooting activities.
Implementation Technologies
SCADA Systems: Supervisory Control and Data Acquisition systems provide comprehensive data collection capabilities for large-scale industrial operations. Modern SCADA platforms integrate with diverse communication protocols and provide centralized data management.
Industrial IoT Platforms: Specialized IoT platforms designed for industrial environments provide scalable data collection, processing, and integration capabilities. These platforms often include device management, security, and analytical features.
Database Technologies: Time-series databases optimized for industrial data provide efficient storage and retrieval capabilities for high-frequency measurement data. These databases support both real-time queries and historical analysis requirements.
Security and Cybersecurity
Network Security: Industrial data collection systems require comprehensive cybersecurity measures including network segmentation, access control, and intrusion detection. Security architectures must protect operational systems while enabling necessary data access.
Data Encryption: Sensitive operational data requires encryption during transmission and storage to prevent unauthorized access and maintain confidentiality. Encryption implementations must balance security against performance requirements.
Access Control: Role-based access control systems ensure that only authorized personnel can access operational data based on job responsibilities and security clearances. Audit trails track data access for compliance and security monitoring.
Best Practices and Implementation Guidelines
- Conduct comprehensive data source assessment to understand collection requirements and system capabilities
- Design scalable collection architectures that can accommodate future expansion and technology evolution
- Implement systematic data quality procedures including validation, calibration, and error handling
- Plan for network reliability and redundancy to ensure continuous data collection capabilities
- Establish data governance policies that define ownership, retention, and access requirements
- Maintain comprehensive system documentation including data dictionaries, interface specifications, and procedures
Integration with Analytical Systems
Industrial data collection serves as the foundation for time series analysis and real-time analytics applications. The collected data enables predictive maintenance programs and anomaly detection systems.
Integration with digital twin implementations requires high-quality, real-time data feeds that maintain synchronization between physical and virtual systems. Data integration platforms consolidate collected data with enterprise systems and external sources.
Performance and Scalability Considerations
Data collection system performance depends on factors including data volume, collection frequency, network capacity, and processing requirements. Scalable architectures leverage distributed processing, load balancing, and efficient storage strategies to handle growing data requirements.
Bandwidth optimization techniques including data compression, intelligent sampling, and edge processing help manage network utilization while maintaining data quality. Storage optimization strategies balance performance against cost for long-term data retention.
Related Concepts
Industrial data collection closely integrates with sensor data processing and telemetry data systems. The capability supports monitoring applications and Industrial Internet of Things implementations.
Industrial architecture design must accommodate data collection requirements including network infrastructure, computing resources, and security considerations. Event driven architecture patterns enable responsive data collection and processing workflows.
Industrial data collection represents a fundamental capability for modern manufacturing that enables data-driven operations, predictive analytics, and continuous improvement. Success requires careful attention to system design, data quality, and integration with operational workflows to realize the full potential of operational data in driving efficiency, quality, and competitiveness.
What’s a Rich Text element?
The rich text element allows you to create and format headings, paragraphs, blockquotes, images, and video all in one place instead of having to add and format them individually. Just double-click and easily create content.
Static and dynamic content editing
A rich text element can be used with static or dynamic content. For static content, just drop it into any page and begin editing. For dynamic content, add a rich text field to any collection and then connect a rich text element to that field in the settings panel. Voila!
How to customize formatting for each rich text
Headings, paragraphs, blockquotes, figures, images, and figure captions can all be styled after a class is added to the rich text element using the "When inside of" nested selector system.